How TE Connectivity Addresses the Unprecedented Challenges of Modern Manufacturing
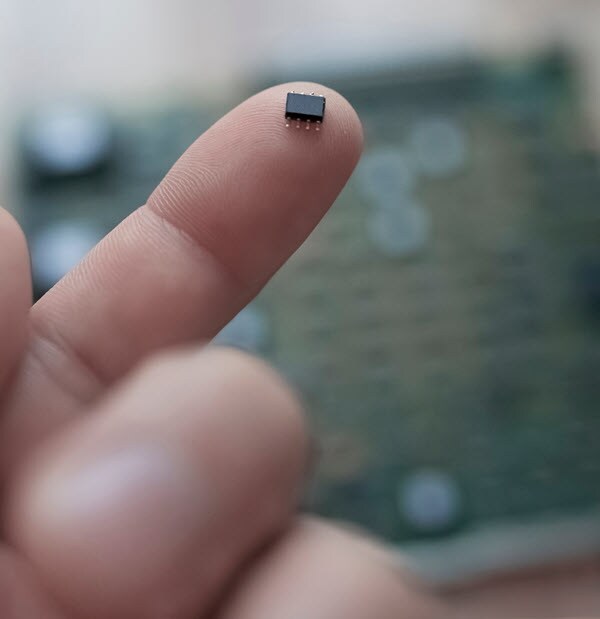
(Source: Elena - stock.adobe.com)
We are in the midst of a new manufacturing renaissance.
The earliest days of the Fourth Industrial Revolution—or Industry 4.0—introduced us to the potential of automation. Through devices such as programmable logic controllers, businesses were able to considerably streamline their manufacturing processes. Yet these systems were largely islands of automation—disconnected individual stations unable to effectively communicate with one another, substantially limiting their effectiveness.
The proliferation of the Industrial Internet of Things (IIoT) changed this. Data flows seamlessly across a network of interconnected stations, sensors, and platforms. Through monitoring and analytics, manufacturers gain deeper insight into their systems and processes than ever before by identifying bottlenecks, addressing system issues, and uncovering opportunities for optimization.
A New Leg of the Journey: Miniaturization
Yet even this hyperconnectivity is simply another phase in the evolution of Industry 4.0. As technology continues to evolve, manufacturing finds itself aligning with the aerospace, automotive, MedTech, and even consumer electronics sectors in a shift towards miniaturization. The drive to make things smaller and ultimately more powerful.
That’s something most people tend to overlook when the topic of miniaturization comes up. It’s not simply about making things smaller for the sake of it. It’s about making things smaller so we can get more out of them.
The potential applications of such an initiative in manufacturing alone are nearly infinite:
- Improved factory automation controls
- Better warehouse automation systems
- Advanced industrial robotics
- Enhanced connectivity and data transmission
- Greater support for the manufacturing of miniaturized products.
The Sum of Its Parts
As with the transition towards automated manufacturing, the mini-movement for connectors has been happening for some time. For years, it has been a matter of efficiency, a means by which factory designers can do more with less. Yet as we move inexorably towards even further miniaturization, it’s rapidly becoming a matter of necessity. Therein lies the problem.
Devices resident on the factory floor must transmit and receive vast amounts of data in harsh industrial environments. They must be capable of surviving extreme heat, intense cold, immense pressure, jarring vibration, and crushing pressure. Regardless of environmental conditions, connectors must maintain their electromechanical integrity even after multiple mating cycles.
More importantly, they must achieve this as inexpensively as possible.
That poses a challenge where ruggedization is concerned. Hardening a system or sensor to withstand extreme conditions traditionally means adding not-inconsiderable bulk to that system. Yet as we’ve already established, miniaturization in modern manufacturing is a necessity. Factory automation designers must constantly miniaturize to improve efficiency and do more with less.
Here’s where TE Connectivity (TE) comes in. For more than 75 years, TE has been a global industrial technology leader in creating a safer, more sustainable, more productive, and more connected future (which are hallmarks of Industry 4.0). TE’s connectivity and sensing products have a proven track record of rugged performance in the harshest environments while meeting the industry’s drive for smaller and smaller components.
I recently sat down with TE Connectivity’s Sameer Trikha, Sr. Mgr. Product Management, Industrial, and Jana New, Americas Product Manager, Industrial, to discuss how TE Connectivity addresses the unprecedented challenges of Industry 4.0. The following sections outline TE’s approach to Industry 4.0 and their featured miniaturized connectors designed to support this phase of the industrial revolution.
Smaller, Better, Faster, Stronger
TE launched a new series of connector solutions designed specifically to address the unprecedented challenges of miniaturized manufacturing. From the start, we knew we needed to provide the same capabilities and patented technologies that made their original connectors reliable without sacrificing scalability, durability, or functionality.
This recognition culminated in the release of our Micro-MaTcH line, which eliminates the need for costly gold-plated connection points, and offers pitch ranges as low as 1mm. We’ve already rolled out many solutions in this new miniaturized niche, aiming to provide robust, cost-effective technology for as many sectors as possible. Our core applications in that regard include:
- Industrial controls
- Building and home automation devices
- Servo drives
- Programmable Logic Controllers (PLC)
- IO devices
- Industrial robotics
- Instrumentation and test equipment
- Telecommunication equipment
- Transportation technology
- Communication hardware
With our September 2021 acquisition of ERNI Group AG, we also recently expanded into several new markets. As a leading manufacturer of high-speed, fine-pitch connectors, ERNI’s addition to our portfolio not only closes several gaps within it, but considerably strengthens our own industrial automation capabilities. Leveraging ERNI’s technology and expertise, we can expand into new sectors including aerospace, automotive, industrial, and medical.
The Power of TE Connectors
As mentioned, we’ve released several new connector solutions developed with miniaturization in mind. The easiest way to drill down to what makes them unique and establish our specific role in Industry 4.0 is to take a quick look at each. There are three in total.
The first two, AMPMODU Small Centerline and AMPMODU 50/50 will see their most frequent use in PLCs, industrial automation, data centers, and IIoT. The latter, Micro-MaTcH, is intended for cost-constrained situations and use cases.
AMPMODU Small Centerline
Containing support for up to 100 positions of 1.0 amps each, this family of connectors features a 1.0mm centerline, and takes up approximately 85 percent less space than traditional connectors. Their robust design includes non-protrusive hold-downs, which both provide retention during soldering and long-term strain relief during high mating cycles.
AMPMODU 50/50
Used in board-to-board and cable-to-board applications, connectors in the AMPMODU 50/50 family feature 1.27mm pitches, 30µ gold plating, and polarization to protect against incorrect mating. Expected to expand considerably in the future, this family includes a series of surface mounted, double row, vertically mounted units, and feature dual-beam contact—not typically seen in connectors of this type. They can carry up to 3.0 amps and operate over an exceptionally wide -65ºC to 105ºC temperature range.
Micro-MaTcH
Designed with cost-constrained applications in mind, this group of patent-protected connectors does not feature gold coating. Ordinarily, this would open the door to fretting brought on by micro-movements from vibration, thermal expansion, or thermal contraction. Fretting often results in poor electrical connection, representing a leading cause of system failure.
TE prevents fretting via a positioning spring within the female contact. This unique mechanism creates a gas-tight connection between connector and receptacle, halting the aforementioned micro-movements. No other company has yet been able to replicate this patented innovation as effectively as TE.
Conclusion
The Fourth Industrial Revolution is here, and miniaturization represents the next major evolution of Industry 4.0. TE intends to play a major role in seeing that evolution through. With an ever-growing, robust portfolio of high-quality connector solutions—such as the AMPMODU Small Centerline with its 30µ gold plating contact option, the AMPMODU 50/50 series suitable for high-density requirements, and the newly developed and unique, gold-free Micro-MaTcH family of connectors and cables—and an approach to miniaturization that doesn’t sacrifice the quality of TE’s original design, TE is well-positioned to be your one-stop-shop for all your engineering interconnect needs.
About the Author
More Content by TE Connectivity